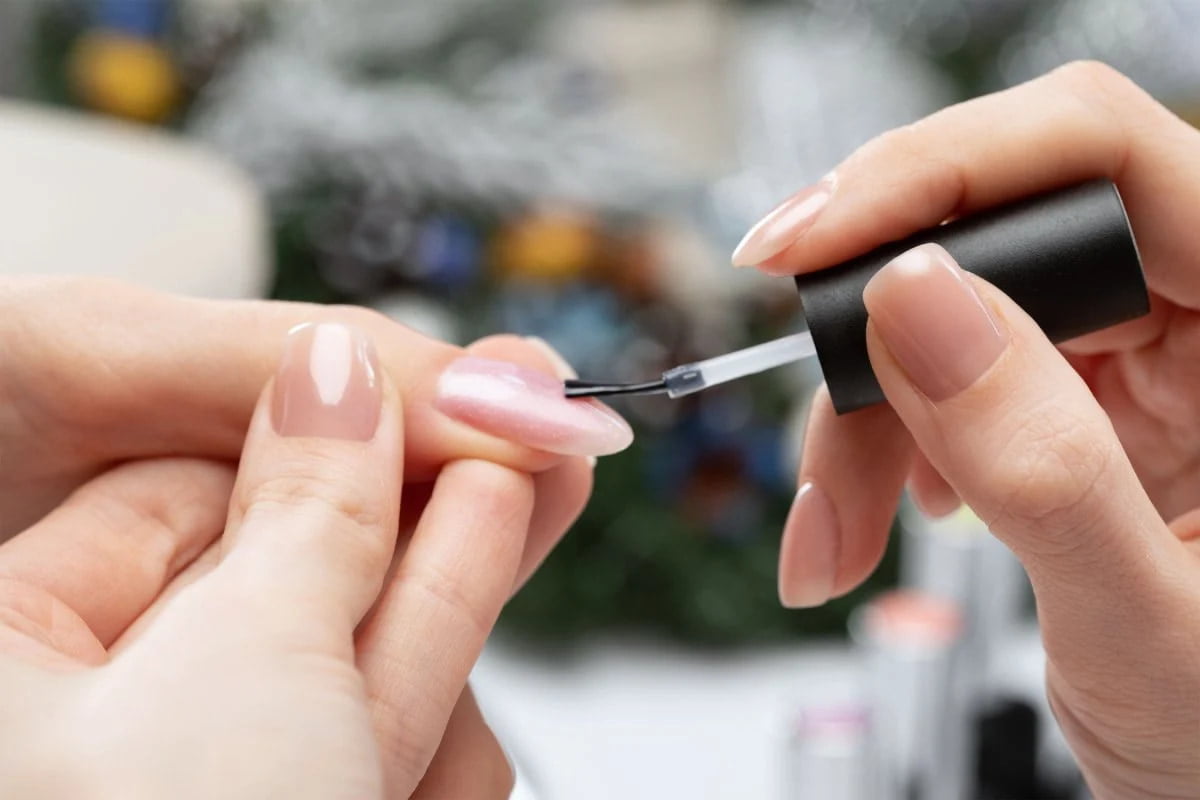
The ‘top coat’ of modern UV-curable nail treatments is essential for providing a glossy, wear-resistant finish to a manicure. But how did modern top coat formulations come about? We take a look at two key innovations that underpin the popularity of top coats today – rapid UV curing and non-yellowing formulations.
The role of gel-based top coats
In the last couple of decades, UV-curable gel-based nail treatments have overtaken conventional air-dried lacquers in popularity, thanks to their ease of application and removal, wide range of colours and effects, and resistance to everyday wear and chipping.
These gels are usually based on methacrylate chemistry and comprise a mix of monomers and oligomers chosen to produce an easily-applied gel-like consistency. Exposure of the formulation to UV-A light (typically 340–380 nm) causes the photoinitiator within the formulation to release radical species, which drive the polymerisation process and harden the gel.
Modern gel-based nail treatments use this fundamental chemistry within three main components, applied in sequence: the ridge-filling and nail-protecting base coat, the colour-imparting colour coat, and a wear-resistant top coat. The top coat is essential for providing durability to the nail by reducing chipping and scratching, and also for providing a desirable gloss finish.
Modern gel-based nail coatings use a base coat, one or more layers of a colour coat and top coat (in that order), with the top coat providing the desired gloss and durability.
The drawbacks of conventional lacquers
However, one area in which these new UV-curable formulations could be used was in the top coat, which of course by necessity had to be colourless. In researching this field for our upcoming product launch, a patent published in 1995 (‘Quick-drying nail coating method and composition’, US5435994) caught our eye. It appears to be the first example of a UV-curable top coat – and thus, really, the start of the whole field.
The author of the patent, bio-organic chemist Vivian B. Valenty, starts by outlining the drawbacks of conventional lacquers, particularly the restrictions imposed by air-drying. She describes how “during the drying period, which can take as long as several hours, women have to refrain from tasks that might cause them to mar this painstakingly, and sometimes expensively, applied nail polish”.
The development of box-like air dryers improved matters somewhat, she explains, but they were still ineffective because they can only dry the surface of the coating and not the lower layers, meaning additional air exposure is required to achieve full strength.
Following a description of various attempts at resolving this issue – including post-application treatments and novel formulations of doubtful utility – Valenty references a patent by James T. Guiliano from 1986 (‘Artificial nails’, US4596260), in which a known photopolymerisable composition is used to adhere preformed artificial nail tips to natural nails, using UV curing. Although the exact use is different from the top coat application that Valenty then focuses on, it appears that this provided the initial inspiration for UV curing of top coats.
Developing a UV-curable top coat
At the time (the early 1990s), Valenty was focusing on methacrylates, as these have a lower potential for skin irritation. In the patent, she describes the discovery of a methacrylate monomer system that, in the presence of nitrocellulose, cured well upon brief exposure to UV light. In addition, it was found that a hard coat could be obtained by using only monofunctional monomers, instead of the mix of monofunctional and difunctional monomers previously described in the field.
The patent then goes on to describe 10 example formulations using ethyl methacrylate and cyclohexyl methacrylate as photoreactive monomers, followed by a further five examples that (at least in part) resolved issues with odour and discolouration, either by replacing the monomers with less volatile equivalents and/or by increasing the proportion of antioxidant while lowering the proportion of photoinitiator.
Importantly for the future application of the technology, the UV lamp used was only 10 W, compared to the 100 W lamp exemplified in the 1986 patent, reducing the risk of skin damage associated with UV exposure. Not only that, but the top coat cured hard within just 3 minutes of exposure, was compatible with commercial nail lacquers of any colour, and could be removed by standard acetone-based polish removers. So in our view at least, this work really paved the way for what was to come.
UV-curable nail treatments take much less time than the drying regimes needed for conventional solvent-based lacquers, and a key development was the use of low-power UV lamps.
The problem of nail yellowing
If there is one criticism to be had over this early UV-curable composition developed by Valenty, it is that, like conventional nail lacquers, it used a substantial quantity of nitrocellulose (preferentially in the range 17–23 wt%). This is unsurprising, as nitrocellulose is soluble in organic solvents and has relatively good adhesion to the nail plate, making it a good choice for nail polish.
However, as was recognised at the time, nitrocellulose-based formulations tend to cause yellowing of the nail, because the nitrocellulose reacts with water to produce nitric acid, which acts upon keratin in the nail to produce yellow or brown oxidation products.
Although Valenty in her 1995 patent made some efforts to minimise this yellowing, clearly the only guaranteed way of avoiding it is to create a formulation free from nitrocellulose. So it was interesting to uncover an early example of this concept in action, in a patent by Sunil J. Sirdesai and George Schaeffer published in 1998 (‘Non-yellowing rapid drying nail polish top-coat compositions’, US Patent 5,785,958).
Replacing nitrocellulose in nail coating formulations
In this work, Sirdesai and Schaeffer first describe the general state of the art, mentioning various attempts to resolve the problem of lengthy drying times. They then go on to highlight previously published examples where cellulose acetate butyrate (CAB) was used as a partial or complete replacement for nitrocellulose, although it’s clear that these had limited success (and one of them even introduced the toxic solvent toluene as an essential component).
Both nitrocellulose and cellulose acetate butyrate (CAB) have a polysaccharide framework, but the structural similarities end there. The nitrocellulose used in top coats typically contains nitrate groups and hydroxyls in a ratio of about 2:1, as illustrated here. In CAB, the relative proportions of the butyrate, acetate and hydroxyl substituents may vary substantially; the structure with a 3:2:1 ratio represented here is just one of many that is used in nail top coat formulations.
The formulation they propose in the patent comprises CAB as a base resin, along with a methacrylate film-former, a mix of mono-, di- and trifunctional methacrylates as cross-linkers, an initiator, and solvents. They say that the amount of CAB could vary substantially, but was preferentially between about 10 and 30 wt%, depending on the exact grade. An interesting aspect of the composition was the ability to cure it using either UV light or a 55 W heat lamp, in conjunction with a photoinitiator or thermal initiator, respectively.
As they go on to explain, the new formulation worked well. With about 3 minutes of curing, a top coat was produced that was resistant to accidental denting or smearing, with full strength being achieved after about 10 minutes.
The authors conclude “Unlike the commercially available top coats that have yellowing or discolouration problems or contain a toxic component in their compositions, the invention provides a non-yellowing, non-toxic, hard, durable and glossy top-coat composition”. To us, the choice of UV or thermal curing is also a key innovation, not least because it gives nail technicians the ability to choose the best system for the job.
The continuing evolution of top coats
By looking back at the history of top coats, we hope we’ve illustrated that the products available today lean heavily upon innovations made decades ago – innovations underpinned by a deep knowledge of the chemistry behind top coat formulations.